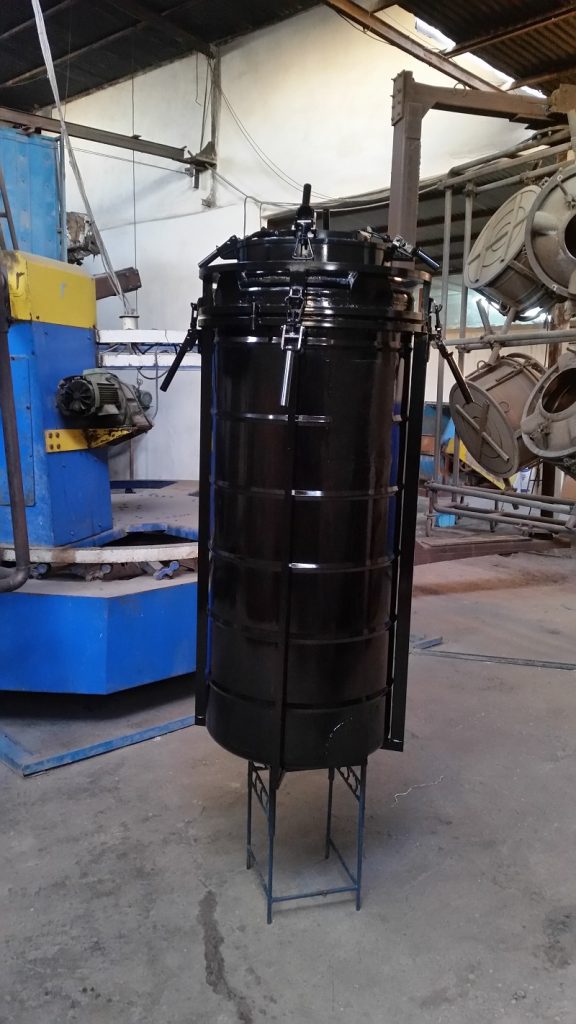
تعریف قالب گیری دورانی
قالب گیری دورانی، روتومولدینگ، روتومولد یا روتوکستینگ یک فرآیند تولید برای تشکیل قطعات توخالی با اندازه نامحدود است. این تولید، یک روش مقرون به صرفه برای تولید قطعات پلاستیکی بزرگ است. مواد پلیمری به قالبی هم عمودی و هم افقی اضافه میشوند که گرم میشود و به آرامی میچرخد،. گرمایش و چرخش همزمان مواد پلیمری را در سطوح داخلی قالب توزیع و ذوب می کند. نتیجه محصولی است که شامل قطعات بدون درز با ضخامت دیواره یکنواخت با مواد بیشتر در گوشهها برای جذب ضربهها و تنشها در جاهایی است که بیشتر اتفاق میافتد.
مواد قالب گیری دورانی
در سال 1961، اولین پودر پلی الفین، پلی اتیلن با چگالی کم، به طور عمومی به صنعت قالب گیری دورانی نشان داده شد. پلی اتیلن ها به دلیل پردازش پذیری، دامنه وسیع خواص و هزینه کم، یکی از محبوب ترین مواد برای قالب گیری روتوم هستند. تامین کنندگان عمده مواد خام ترموپلاستیک پودرهای فرموله شده ویژه برای قالب گیری دورانی، از جمله پلی پروپیلن، نایلون، پلی کربنات، پلی وینیل کلرید سفت و سخت و غیره را بررسی کرده اند. این پودرها را می توان فوم کرد یا با فایبر گلاس تقویت کرد. علاوه بر تامینکنندگان مواد خام، بسیاری از قالبگیران دورانی نیز از خدمات سنگزنی سفارشی استفاده کردهاند یا قابلیتهای آسیاب درون کارخانه خود را دارند که انتخاب مواد را برای این فرآیند نیز افزایش داده است.
معرفی قالب گیری دورانی
این مقاله تمام اطلاعاتی را که باید در مورد قالب گیری دورانی بدانید ارائه می کند. بیشتر بخوانید و در مورد موارد زیر بیشتر بدانید:
مروری بر قالب گیری دورانی و تاریخچه آن
انواع ماشین های قالب گیری دورانی
فرآیندهای قالب گیری دورانی
مواد مورد استفاده در قالب گیری دورانی
و خیلی بیشتر…
قفس مرغ قالبی دورانی
قالب گیری دورانی
قالب گیری دورانی که معمولاً به آن “روتومولدینگ” گفته می شود، یک تکنیک ریخته گری پلاستیک است که برای تولید قطعات بزرگ توخالی، بدون درز و دو جداره استفاده می شود. این یک فرآیند سه مرحله ای است که شامل یک قالب روی یک قاب چرخان، یک محفظه گرمایش و یک محفظه خنک کننده است. قالب های فرآیند روتومولدینگ به طور ویژه طراحی شده اند و قابلیت تولید محصولات تک جداره و دو جداره را دارند.
ماده اولیه اصلی برای قالب گیری روتوم یکی از مواد پلیمری های پلی اتیلن است که برای شروع فرآیند در قالب بارگذاری می شود. در محفظه گرمایش، قالب در حین گرم شدن می چرخد. قاب قالب قادر است قالب را به هر نقطه از محور دورانی خود بچرخاند. همانطور که قالب می چرخد، مواد پلیمری روی سطح داخلی قالب پخش می شود و به محصول نهایی ضخامتی برابر و یکنواخت در سراسر سطح آن می دهد.
پس از مدت زمان معینی، قالب از محفظه گرمایش به محفظه خنک کننده منتقل می شود، جایی که مواد پلیمری ذوب شده مایع قبل از بیرون ریختن محصول پلاستیکی از قالب اجازه داده می شود تا خنک شود. محصولات قالب گیری دورانی از بالاترین کیفیت برخوردار بوده و به دلیل دوام و استحکام شناخته شده اند.
فرآیند قالب گیری دورانی پایه
قالبگیری دورانی یک فرآیند قالبگیری بدون فشار است که باعث میشود ابزارهای قالبها ارزانتر باشند زیرا مجبور نیستند فشار ناشی از فشار را تحمل کنند. اندازههای محصولات قالبگیری دورانی نامحدود است زیرا قالبها و تجهیزات قادر به ایجاد اشکال پلاستیکی بسیار بزرگ هستند. همچنین محدودیت های کمی در مورد طراحی قطعات وجود دارد که به طراح آزادی می دهد تا جزئیات پیچیده را اضافه کند.
از جمله محصولات تولید شده توسط قالب گیری دورانی می توان به کایاک، کلاه ایمنی ورزشی، مانکن های نمایشی، مخازن ذخیره آب، تخت نوزاد و موانع برای ساخت و ساز جاده اشاره کرد. همه این محصولات پلاستیکی بزرگ را می توان به راحتی با استفاده از قالب گیری دورانی با هزینه کمتر و با کارایی بالا تولید کرد.
فرآیند قالبگیری دورانی به مصریان باستان برمیگردد که صدها سال پیش سرامیک را خلق کردند. اولین کاربرد فرآیند قالب گیری دورانی پیشرفته تر، تولید گلوله های توپخانه در سال 1855 و تخم مرغ های شکلاتی توخالی توسط سوئیس ها در سال 1910 برای ایجاد ضخامت و تراکم دیواره یکنواخت بود. در این دوره ها، چندین اختراع ثبت شده بود تا ماهیت این فرآیند ریخته گری را مستند کند. با این حال، به عنوان یک روند کند تلقی می شد و با چالش هایی مواجه شد که منجر به رایج نشدن این روند شد.
قالب گیری دورانی سفارشی
در طول دهه 1940، این فرآیند برای ایجاد سر عروسک و سایر اسباببازیهای کوچک از مواد پلیمری پلاستیزول پلیوینیل کلرید با استفاده از پلاستیک نیکل مسی الکتروشکلشده استفاده شد. راه اندازی فقط شامل موتورهای الکتریکی و مشعل های گازی بود و قسمت تمام شده با آب سرد خاموش شد. این روش باعث شده است که بسیاری از صنایع در فرآیند تولید خود از این روش استفاده کنند که منجر به ساخت مخروطهای جادهای، شناورهای دریایی و دستههای بازو شد.
امروزه از قالبگیری دورانی در کاربردهای مختلفی استفاده میشود و قطعات بزرگتر و پیچیدهتری تولید میکند. ماهیت فرآیند بهتر درک می شود و طراحی تجهیزات به طور قابل توجهی افزایش یافته است. چرخه های طولانی گرمایش و سرمایش همچنان یک گلوگاه بزرگ برای برخی از تولیدکنندگان است. این توسعه بر اصلاح تجهیزات قالب گیری دورانی توسط توسعه دهندگان برای تطبیق با افزایش تقاضا متمرکز شده است.
انواع ماشین های قالب گیری دورانی
راهاندازی استاندارد عملیات قالبگیری دورانی شامل یک بازو یا گهواره است که قالب، اجاقهای منفرد یا چندگانه و اتاقهای خنک کننده را حمل میکند. تنها تفاوت بین ماشین ها در جهت حرکت قالب است که دنباله ای از فرآیند قالب گیری دورانی است. انواع ماشین های مورد استفاده در فرآیند قالب گیری دورانی به شرح زیر است:
ماشین تاشو:
ماشین های تاشو ماشین های تک ایستگاهی هستند که قالب گیری و خنک سازی در یک محفظه انجام می شود. قالب با مواد پلیمری از طریق پانل جلویی در محفظه بارگیری و تخلیه می شود. پانل جلویی و پوشش در هنگام گرم کردن و قالب گیری قفل می شوند. پس از قالبگیری، درب آن باز میشود تا خنک شود و باعث میشود قالب از فر باز شود.
برجک یا ماشین چرخ و فلک:
ماشین های برجک در یک محور مرکزی می چرخند و دارای سه تا شش بازو هستند. هر بازو دارای قالبی است که به انتهای خود متصل است و به ترتیب فرآیند قالب گیری دورانی، از بارگیری، گرمایش، خنک سازی و تخلیه، در طول چرخش چرخ فلک از ایستگاه ها عبور می کند. آن ها ماشین های دورانی هستند که با استفاده از یک رابط MMI با یک کنترل کننده منطقی قابل برنامه ریزی (PLC) کار می کنند.
ماشینهای قالبگیری دورانی میتوانند از سه تا شش بازو داشته باشند که هر بازو در یکی از سه مکان فرآیند قرار میگیرد. آن ها در طرحهای بازوی ثابت و مستقل، با مدلهای بازوی مستقل میتوانند بازوهای بیشتری داشته باشند که به طور جداگانه حرکت میکنند و امکان استفاده از قالبهای بیشتر و قالبهایی با اندازهها، گرمایش و ضخامتهای متفاوت را فراهم میکنند.
بازوهای یک ماشین قالب دورانی مستقل از هاب مرکزی، دمای اجاق یا زمان ماندگاری موتوردار و کنترل می شوند. برجک در پایان هر چرخه 120 درجه می چرخد، به موقعیت بعدی حرکت می کند و همه بازوها همیشه در یک موقعیت هستند و هرگز بیکار نیستند.
دستگاه چرخ فلک
ماشین شاتل:
ماشین های شاتل دارای بازوهای مستقلی هستند که به صورت دو محوره می چرخند و قالب را از بارگیری، خنک کننده و تخلیه (ایستگاه های ترکیبی) به محفظه گرمایش واقع در وسط مسیر حرکت می دهند. پس از اتمام فرآیند، قالب به موقعیت اولیه خود باز می گردد. ماشین های شاتل در به حداکثر رساندن فضای کف سودمند هستند.
این سیستم به جای اینکه منتظر بماند تا یک قالب قبل از شروع چرخه جدید خنک شود، قالب های جداگانه را به طور مداوم اجرا می کند. پلاستیک به قالب اول تزریق می شود و قالب دوم را در موقعیت خود قرار می دهد. با سرد شدن قالب اول، قالب دوم را گیره میکنند و پلاستیک را داخل آن تزریق میکنند و برای خنک شدن میفرستند. زمانی که قالب دوم برای خنک شدن فرستاده شد، قالب اول آماده شروع فرآیند است.
توسعه روش شاتل در پاسخ به زمان تلف شده در طول خنک شدن قالب ها بود که می تواند بازدهی کاهشی داشته باشد. ایده پشت این فرآیند این است که از زمان خنک شدن استفاده کرده و آن را مولد کنید. جدا از مزایای زمانی، ماشین های قالب گیری شاتل صرفه جویی قابل توجهی در هزینه ها ایجاد می کنند.
قالبهای فرآیند شاتل به همان روشی توسعه مییابند که قالبهای استاندارد هستند، اما باید مهندسی شوند تا ابعاد فرآیند قالبگیری شاتل را برآورده کنند. ابزار استاندارد است، با محدودیتهای کمی که برای برآورده کردن شرایط قالبگیری شاتل ضروری است.
Swing Machine:
چرخاننده ها نیز دارای بازوهای مستقل هستند، اما در این نوع، برای کار با تمام بازوها نیازی نیست، به این معنی که می تواند به راندمان تولید کمک کند. بازوهای نصب شده در گوشه فر به صورت دو محوره می چرخند و قالب را از محفظه گرمایش به سمت اتاق خنک کننده می چرخانند. ماشین های چرخش ممکن است تا چهار بازو داشته باشند. آن ها برای موادی با زمان خنک سازی و قالب گیری طولانی در مقایسه با زمان گرمایش مناسب هستند.
برخی از دستگاه های قالب بازوی دورانی دارای دو بازو به گوشه فر هستند به طوری که دستگاه دارای چهار بازو با دو نقطه محوری است. ماشین ها می توانند به طور مداوم کار کنند و نیازی به توقف برای تعمیر و نگهداری یا نصب قالب های جدید ندارند.
دستگاه چرخش
ماشین چرخ عمودی:
ماشین های چرخ عمودی مانند چرخ و فلک عمل می کنند. قالب ها در یک گهواره قرار می گیرند و در طول چرخش آن از بارگیری به تخلیه، گرمایش و سرمایش منتقل می شوند. ایستگاه تخلیه و بارگیری در پایین چرخ و بین قسمت های سرمایش و گرمایش قرار دارد. ماشین های چرخ عمودی می توانند قطعات کوچک تا متوسط را قالب گیری کنند.
ماشین عمودی
دستگاه راک اند رول: دستگاه های راک اند رول نیز دارای قالب هایی هستند که در گهواره قرار دارند. گهواره 45 درجه به جلو و عقب در یک محور افقی، 45 درجه یا پایین تر از افقی می چرخد، در حالی که 360 درجه بر روی یک محور عمود می چرخد. ماشینهای راک اند رول قطعات بلند با قطرهای کوچک مانند کانو و کایاک تولید میکنند.
ماشین های راک اند رول دارای دو بازو هستند که هر بازو یک چرخش 360 درجه در یک جهت انجام می دهد. وقتی بازوها می چرخند، به جلو و عقب تکان می خورند تا پلاستیک به طور یکنواخت در قالب پخش شود. برای افزایش بهره وری فرآیند، قالب ها قبل از بارگیری گرم می شوند.
فرآیند قالب گیری دورانی
مراحل انجام عملیات قالب گیری دورانی به شرح زیر است:
مواد پلیمری پودر شده
آسیاب یا پودر کردن برای تبدیل گلوله ها یا پودرهای درشت به پودر ریز یا بسیار ریز استفاده می شود. اندازه ذرات هر دستگاه متفاوت است، که مستلزم آن است که مواد پلاستیکی از چندین پودر کننده عبور داده شود تا قوام مناسب حاصل شود. روشهای مختلف پودر کردن شامل پودر کردن دستهای، آسیاب یا آسیاب خشک یا پودر کردن مرطوب است. انتخاب روش پودرسازی بستگی به نوع فرآیند قالب گیری دارد که پلاستیک پودر شده روی آن اعمال می شود.
مواد اولیه برای قالب گیری روتوم بسته به خواص فیزیکی و کاربردهای مورد نظر متفاوت است. افزودنی ها و رنگ ها برای دستیابی به ویژگی ها و خواص مورد نیاز اضافه می شوند. انواع مختلف پلی اتیلن عمدتاً برای فرآیند روتومولدینگ استفاده می شود و ترموپلاستیک هایی هستند که به راحتی می توان با حرارت دادن آن ها را تغییر شکل داد. پنج نوع پلی اتیلن عبارتند از: پلی اتیلن خطی با چگالی کم (LLDPE)، پلی اتیلن با چگالی متوسط (MDPE)، پلی اتیلن با چگالی بالا (HDPE)، پلی اتیلن با چگالی کم (LDPE) و پلی اتیلن متقاطع (XLPE).
بارگیری: مقدار اندازه گیری شده پلیمر که به صورت پودر مواد پلیمری است در قالب توخالی قرار داده شده و محکم می شود. مواد پلیمری پودری باید در اندازه های ریز، همگن و خشک شده باشد تا جریان خوبی داشته باشد و از تشکیل حباب جلوگیری شود. میزان بارگذاری مواد پلیمری یکی از عواملی است که ضخامت دیواره قطعه را تعیین می کند.
بارگیری مواد پلیمری
قالب توخالی از آلومینیوم ریخته گری یا ورق فولادی ساخته شده و به قسمت قالب گیری شکل خود را می دهد.
عامل رهاسازی قالب، پوششی است که روی دیواره های داخلی قالب وجود دارد. برای حذف موثر قسمت قالب گیری شده پس از سرد شدن استفاده می شود، زیرا از چسبیدن به سطح قالب جلوگیری می کند. انواع مواد رهاساز قالب به شرح زیر است:
پوشش قربانی قالب گیری دورانی:
این نوع ماده آزادکننده قالب که معمولاً سیلیکون است، هنگام رها شدن از ابزار با قسمت قالب گیری جدا می شود. از این رو، در شروع هر فرآیند بارگذاری اعمال می شود.
پوشش نیمه دائمی: مواد رهاسازی قالب نیمه دائمی معمولاً در بیشتر صنایع استفاده می شوند. پس از چندین سیکل گرمایش و خنک سازی پلیمر دوام می آورد. قبل از مصرف مجدداً اعمال یا شارژ می شود.
پوشش دائمی قالب گیری دورانی:
این روش نیاز به استفاده مجدد از ماده آزاد کننده قالب را از بین می برد، زیرا به طور دائم بر روی سطح قالب ثابت می شود. با این حال، لایه عامل رهاسازی قالب دائمی می تواند به دلیل خراشیدگی و استفاده نادرست از بین برود. رایج ترین پوشش دائمی عامل رهاسازی کپک پلی تترا فلوئورواتیلن (PTFE) است.
حرارت دادن قالب گیری دورانی:
مواد پلیمری پودر شده در داخل قالب توخالی گرم می شود در حالی که به آرامی می چرخد تا تمام مواد پلیمری ذوب شود. با ذوب شدن مواد پلیمری، تمام دیواره داخلی قالب را می پوشاند. عمل همزمان حرارت دادن و چرخش توزیع یکنواخت مواد پلیمری در داخل قالب را تضمین می کند. قالب به صورت دو محوره می چرخد و معمولا کند است.
برای دستیابی به توزیع ضخامت دیواره مناسب، باید نسبت چرخش مناسب تعیین شود. این مقدار تعداد چرخش در دقیقه (RPM) در محور افقی بیش از RPM در محور عمودی است. کره ها یا مکعب ها را می توان با نسبت چرخش 4:1 قالب گیری کرد. برای جامدات نامنظم، بسته به اینکه سازنده چگونه این فاکتور را بهینه کرده است، نسبت باید 1:8 یا 8:1 باشد.
زمان حرارت دهی پلیمر حیاتی است و یکی از پارامترهایی است که کیفیت قطعه تمام شده را تعیین می کند. زمان گرمایش بیش از حد منجر به تخریب حرارتی پلیمر می شود و خواص مکانیکی انتهایی مانند مقاومت کمتر در برابر سایش و ضربه را کاهش می دهد. در مقابل، زمان ناکافی حرارت دادن منجر به ذوب ناقص پلیمر می شود. دانه های ذوب نشده با مواد پلیمری مذاب ادغام نمی شوند که منجر به تشکیل حباب می شود. این تنوع اثرات نامطلوبی بر خواص مکانیکی نهایی محصول دارد.
خنک سازی قالب گیری دورانی
در این مرحله پلیمر مذاب داخل قالب سخت شده و به شکل دلخواه خود جامد می شود. قسمت بیرونی قالب دورانی با همرفت طبیعی یا اجباری معمولاً با استفاده از هوا خنک می شود. هوای خنک کننده گاهی اوقات به قسمت داخلی قالب برای حفظ ثبات ابعادی در طول خنک شدن عرضه می شود. ممکن است از اسپری های آب برای کاهش زمان خنک شدن استفاده شود، اما این می تواند خواص مکانیکی و ابعاد قطعه را تحت تاثیر قرار دهد.
زمان سرد شدن پلیمر به اندازه زمان گرمایش بسیار مهم است. بنابراین، سرعت خنک کننده مناسب باید تعیین شود. خنک شدن سریع منجر به تاب برداشتن و انقباض غیرقابل کنترل قطعه می شود. از طرف دیگر خنک شدن آهسته باعث جریان مواد پلیمری مذاب و در نتیجه ضخامت دیواره ناسازگار می شود.
قالب گیری یا تخلیه قالب گیری دورانی
قسمت خنک شده با دقت توسط اپراتور از ابزار قالب توخالی خارج می شود. یک سیستم تخلیه هوا می تواند به بلند کردن قطعه از ابزار کمک کند. پس از جدا شدن قطعات، به فرآیندهای بعدی مانند بازرسی و بسته بندی ادامه می دهد.
فرآیندهای ثانویه قالب گیری دورانی
این می تواند شامل رنگ آمیزی، پوشش، مونتاژ، جوشکاری، افزودن درج و غیره باشد. هر نوع فرآیند ثانویه به کاربرد محصول نهایی بستگی دارد.
پرکننده فوم قالب گیری دورانی
ماشین های قالب گیری دورانی پیشرو
ماشینهای زیادی برای انجام قالبگیری دورانی در ایالات متحده و کانادا وجود دارد. این ماشینها در جامعه امروزی مهم هستند زیرا تولید مقرونبه صرفه و کارآمد محصولات پلاستیکی مختلف را امکانپذیر میکنند و به صنایعی مانند خودروسازی، مبلمان، تجهیزات پزشکی و اسباببازی کمک میکنند.
مواد مورد استفاده در قالب گیری دورانی
پلیمرهای رایج مورد استفاده در قالب گیری دورانی در زیر ارائه شده است. بیشتر پلیمرهایی که برای این فرآیند استفاده می شوند ترموپلاستیک هستند.
پلی اتیلن: پلی اتیلن بیش از 80 درصد پلیمرهای مورد استفاده در صنایعی که از قالب گیری دورانی استفاده می شود را تشکیل می دهد. این مورد به دلیل هزینه کم و سهولت قالب گیری آن است. همچنین برخلاف پلیمرهای غیر پلی اتیلن که به سختی آسیاب می شوند، به صورت پودری در دسترس است. همچنین دارای مقاومت شیمیایی خوب و جذب آب کم است.
گریدهای پلی اتیلن قابل استفاده در چرخش عبارتند از پلی اتیلن با چگالی بالا (HDPE)، پلی اتیلن با چگالی کم (LDPE)، پلی اتیلن با چگالی متوسط (MDPE) و پلی اتیلن با چگالی کم خطی (LLDPE).
پلی پروپیلن
پلی پروپیلن دومین پلاستیک فرآوری شده است و یکی از پرکاربردترین پلیمرهای موجود است. دارای ویژگی های بین LDPE و HDPE است. خواص ارزشمند آن مقاومت شیمیایی، گرما و خستگی خوب است.
پلی وینیل کلراید
پلی وینیل کلراید شکل پلیمری مونومر وینیل کلرید است. این یک پلاستیک محکم و سفت است و با بسیاری از مواد افزودنی برای اصلاح خواص مکانیکی آن سازگار است.
نایلون
نایلون از گروه پلاستیک پلی آمید می آید. جدا از تولید فیلم و الیاف، از این پلیمر می توان به عنوان ترکیب قالب گیری استفاده کرد.
با توجه به ماهیت مراحل فرآیند، الزاماتی در انتخاب پلیمر مورد استفاده برای قالب گیری دورانی وجود دارد. این ترموپلاستیک ها را به روش های زیر محدود می کند:
پلاستیک مذاب در دمای بالا در معرض اکسیژن قرار می گیرد که ممکن است منجر به اکسیده شدن و از بین رفتن خواص مکانیکی مطلوب پلیمر شود. بنابراین مولکول ماده پلیمری باید دارای گروه هایی با خاصیت آنتی اکسیدانی باشد.
پلیمر باید پایداری حرارتی بالایی داشته باشد تا ماده در برابر تغییرات دائمی ناشی از دماهای بالا مقاومت کند.
ماده مذاب باید به راحتی در دیواره های قالب جریان یابد زیرا جریان فقط به حرکت دورانی وابسته است و هیچ فشاری در آن وجود ندارد. ویژگی های جریان پلیمر انتخابی در دماهای بالا باید در مرحله بهینه سازی در نظر گرفته شود.
افزودنی های اولیه خواص مکانیکی قطعه را بهبود می بخشد و به فرآیند قالب گیری کمک می کند. اصلاحکنندههای جریان به جریان مواد پلیمری پلیمری در حالت مذاب برای دستیابی به توزیع ضخامت خوب کمک میکنند. تثبیت کننده های حرارتی از تخریب حرارتی ناشی از دماهای بالا جلوگیری می کنند. پرکننده ها سفتی را افزایش می دهند و اصلاح کننده های ضربه قدرت ضربه را افزایش می دهند. با این حال، مقدار آن باید کنترل شود، زیرا باعث ناهمواری سطح و کاهش جریان می شود. افزودنیهای ثانویه نیز برای دادن ویژگیهای خاص به محصول نهایی مانند رنگها، بازدارندههای شعله و عوامل ضد الکتریسیته ساکن استفاده میشوند.
مزایا و معایب قالب گیری دورانی
مفهوم قالبگیری دورانی مفهومی ساده است، اما در واقع برای برخی از تولیدکنندگان دستیابی به یک محصول خوب خارج از فرآیند چالش برانگیز است. قالب گیری دورانی به دلیل مزایای آن در مقایسه با سایر روش های قالب گیری ارزشمند است. با طراحی و تنظیمات مناسب، سازنده و کاربران نهایی می توانند از مزایای زیر بهره مند شوند:
ضخامت دیوار یکنواخت
ضخامت دیواره ثابت، در تمام اضلاع، لبه ها و گوشه ها، دوام قطعه را افزایش می دهد. با سرعت چرخش مناسب و چرخه های خنک کننده، ضخامت دیواره یکنواخت ممکن است حتی در تولید قطعات دیواره ضخیم به دست آید. گوشهها و لبههای تولید شده با قالبگیری دورانی در مقایسه با قالبگیری دمشی ضخیمتر هستند که مواد مذاب در آن نواحی کشیده میشود.
سهولت در تولید قطعات دوجداره
قطعات دوجداره به راحتی و بدون نیاز به پردازش های ثانویه مانند جوشکاری و ساخت اتصالات ساخته می شوند. قطعات تولید شده دارای لبه های بدون درز هستند که باعث از بین رفتن نقاط تنش و در نتیجه افزایش دوام می شود.
ابزار ارزان قیمت
از آنجایی که قالب مجبور نیست فشارهای بالایی را تحمل کند، می توان آن را با استفاده از مواد ارزان قیمت مانند آلومینیوم تولید کرد. زمانی که فقط دوره های تولید کوتاه مورد نیاز است، سرمایه گذاری کمتری برای ابزارسازی مورد نیاز است.
انعطاف پذیری تولید
قطعات مختلف را می توان همزمان در یک دستگاه قالب گیری کرد. با برخی از تجهیزات قالب گیری دورانی که دارای بازوهای مستقل هستند، مدیریت ابزار را آسان می کند
می توان قطعات بزرگتر تولید کرد، قالب گیری دورانی تولید قطعات توخالی بزرگ را امکان پذیر می کند. تنها محدودیت اندازه اتاق های گرمایش و سرمایش است.
فرآیندهای پایین دست کمتر مورد نیاز و حداقل ضایعات در تولید
قطعه تولید شده در قالب گیری دورانی تنها یک قطعه است. از این رو، نیازی به انجام مراحل پیرایش یا جداسازی نیست. قالبگیری دورانی همچنین باعث اتلاف کمتری از مواد پلیمری به شکل رانر، اسپرو و برش میشود.
سهولت در دکوراسیون: یک طراح می تواند به راحتی جزئیاتی مانند بافت ها و نمادها را از طریق افزودن چنین جزئیاتی بر روی سطح ابزار ترکیب کند.
قالب در گرافیک
از آنجایی که قالب گیری دورانی مزایای زیادی نسبت به انواع دیگر فرآیندهای قالب گیری دارد، به این معنی نیست که برای همه تولیدکنندگان بهترین است. در اینجا برخی از معایب این فرآیند وجود دارد:
زمان و هزینه چرخه بالا
قالب گیری دورانی ممکن است برای تولید با حجم بالا مناسب نباشد. چرخش آهسته در حین حرارت دادن به حالت مذاب و سرد شدن تدریجی قطعه و کل ابزار تا دمای اتاق پس از قالب، زمان زیادی را در طول چرخه قالب گیری مصرف می کند. سیستم های آب خنک کننده یا هوا در دسترس هستند، اما نیاز به هزینه اضافی دارد.
در نهایت، به دلیل در دسترس بودن محدود ویژگیهای اتوماسیون، هنوز مراحل دستی در این فرآیند وجود دارد (مانند قالبگیری). این مورد نیز به هزینه کلی عملیات می افزاید.
گزینه های محدود مواد
تعداد کمی از پلیمرها به عنوان ماده خام برای این فرآیند واجد شرایط هستند زیرا برای پردازش موفقیت آمیز نیاز به تبدیل به فرم پودری دارند. پلیمرهای غیر از پلی اتیلن پرهزینه هستند و آسیاب آن ها دشوار است. همچنین، این فرآیند مستلزم آن است که پلیمر از پایداری حرارتی بالایی برخوردار باشد، که انتخاب مواد پلیمری های پلی پایه را محدود می کند.
عمر کوتاه تر ابزار
از آنجایی که فقط از فلز نازک و نرم ساخته شده است، ابزار باید پس از چندین دوره قالب گیری تعویض شود تا از کیفیت قطعات تولید شده به دلیل عدم تکرارپذیری اطمینان حاصل شود.
قالب گیری برخی از جزئیات و طرح ها دشوار است: ضخامت یکنواخت روی یک سطح صاف بزرگ به دلیل جریان مواد پلیمری به سختی قالب گیری می شود. همچنین ماشین های قالب گیری دورانی قادر به قالب گیری قطعات با تحمل بالا و لبه های تیز نیستند. قالب گیری با فشار بالا ممکن است در نظر گرفته شود.
کاربردهای قالب گیری دورانی
قالب گیری دورانی کاربردهای زیادی مانند قطعات صنعتی و خودرو، مبلمان، تجهیزات حمل و نقل مواد، دستگاه های پزشکی، اسباب بازی ها و موارد دیگر دارد. برخی از محصولات قابل توجه ساخته شده از قالب گیری دورانی عبارتند از:
تجهیزات جابجایی مواد مانند جعبه های بادوام، پالت های قابل انباشته، ظروف و جعبه های عایق که فقط با قالب گیری دورانی تولید می شوند.
مخازن ذخیره سازی پلاستیکی، درام های گالن، و کربوه های حاوی حجم های کوچک تا بسیار زیاد آب و مواد شیمیایی
لوازم آزمایشگاهی و پزشکی مانند سرنگ، ماسک اکسیژن و لامپ فشاری
تخته ستون فقرات
ابزار باغبانی و کشاورزی مورد استفاده برای کاشت، مانند گلدان، سطل، سطل کمپوست و چرخ دستی باغبانی
محصولات بهداشتی مانند ظروف زباله، سطل زباله و سپتیک تانک
وسایل نقلیه دریایی و تجهیزات برای حمل و نقل و ورزش های آبی مانند قایق های پارویی، کانو، بویه و کایاک تولید شده در دستگاه قالب گیری راک اند رول
موانع ایمنی، مخروط های ترافیکی و سایر موارد
شناورها
مشابه موجود در جاده ها و بزرگراه ها
اسباببازیها و تجهیزات ورزشی مانند قطعات عروسک، توپ فوتبال، سرسره زمین بازی، قطعات تجهیزات بدنسازی و وسایل شناور برای استخرهای شنا
پناهگاه ها و مسکن های کوچک (مانند پناهگاه های گردباد، توالت های قابل حمل، امکانات آزمایش)